توانمندی های واحد عملیات حرارتی
- عملیات کربوراسیون گازی با کوره های SIB ایتالیا از نوع Batch Furnace
- عملیات سختکاری با کوره های زمینی (Pit Furnace)
- عملیات حرارتی نرماله، آنیل و تمپرینگ با کوره های Batch Furnace
- عملیات حرارتی سختکاری القایی با کوره های Inducto heat
- جوشکاری قطعات با روش جوش اصطکاکی (FRW) و جوش مقاومتی سر به سر (Flash Butt)
عملیات حرارتی فولادها
سختی و دیگر خواص مکانیکی بسیاری از فولادها و برخی فلزات غیرآهنی را میتوان توسط عملیات حرارتی تغییر داد. فولاد، آلیاژی ساخته شده از آهن و کربن است. درصد جرمی کربن تعیینکننده قابلیت انجام عملیات حرارتی بر روی فولادها است. فولادهای کم-کربن حاوی ۰٫۰۳ تا ۰٫۳ درصد کربن، فولادهای کربن-متوسط حاوی ۰٫۳۵ تا ۰٫۵۵ درصد کربن و فولادهای پر-کربن حاوی ۰٫۶ تا ۱٫۵ درصد کربن هستند (چدنها حاوی بیش از ۲٪ کربن هستند). هرچه کربن فولاد بیشتر باشد قابلیت سختکاری آن بیشتر میشود. فولادهای کم-کربن حاوی مقدار کافی برای سختکاری مؤثر نیستند و باید از روشهای دیگری برای افزایش سختی سطح آنها استفاده کرد(مانند کربورایزینگ و سختکاری القایی). فولادهای کربن-متوسط و پر-کربن را میتوان با روشهای مناسب سختکاری کامل کرد. ("سختکاری کامل" یا Through hardening به معنای سختکاری قطعه تا عمق کامل آن میباشد و در مقابل "سختکاری سطحی" یا Case Hardenning قرار دارد(عمق سختکاری به میزان عناصر آلیاژی آن بستگی دارد.)
الف) سختکاری کامل
کوئنچ کردن
برای سخت کاری فولادهای کربن-متوسط یا پرکربن، ابتدا قطعه را تا بیشتر از یک دمای بحرانی (در حدود ۷۶۰ درجه سلسیوس) گرم کرده و اجازه میدهند برای رسیدن به تعادل مدتی در آن دما باقی بماند، و سپس بهطور ناگهانی آن را به داخل حمامی از آب سرد یا روغن فرو میبرند تا دمای قطعه به دمای محیط برسد. این سرد کردن ناگهانی باعث ایجاد محلولی فوق اشباع به نام «مارتنزیت» میگردد که بسیار سخت میباشد. متأسفانه این فاز بسیار ترد و شکننده است. در حقیقت با افزایش سختی قطعه، استحکام آن کاهش مییابد.
ما در گروه پیشتاز قطعه با استفاده از کوره زمینی (pit furnace)، عملیات سختکاری کامل قطعات را انجام می دهیم.
همچنین بوسیله کوره های (Batch furnace) عملیات ثانویه تمپرینگ، آنیل، نرمالیزاسیون، تنش زدایی و کروی سازی را با دقت بالا انجام میدهیم .
تمپر کردن (برگشت دادن)
پس از عملیات کوئنچینگ میتوان قطعه را دوباره تا دمای کمتری گرم کرده (در حدود ۲۰۰ تا ۷۰۰ درجه سلسیوس)، آن را مدتی در آن دما نگاه داشته و سپس آن را به آهستگی خنک کرد. این کار باعث میشود مقداری از مارتنزیت دوباره به فریت و سمنتیت تبدیل شود. اگرچه اینکار باعث کاهش سختی شده اما میزان داکتیلیته یا قابلیت شکلپذیری قطعه را تا حدودی بازگردانی میکند. با تغییر متغیرهای دما و زمان در این فرایند میتوان انواع مختلفی از فولادها با خواص مختلف تولید کرد. یک مهندس مواد باتجربه میتواند از این طریق فولاد مورد نیاز کاربردهای مختلف را تولید کند.
آنیلینگ (بازپخت )
فرایندهای کوئنچ کردن و برگشت دادن را میتوان توسط بازپخت بازگردانی کرد. قطعه تا دمای بحرانی گرم میشود (مانند فرایند کوئنچ) اما اینبار اجازه داده میشود تا قطعه به آهستگی خنک شود. اینکار باعث بازگردانی شرایط محلول و همچنین خواص مکانیکی قطعه قبل از عملیات سختکاری میشود. معمولاً حتی اگر قطعه سختکاری نشده باشد، برای حذف تنشهای ایجاد شده در حین فرایند شکل دهی و ساخت قطعه آن را بازپخت میکنند. این کار باعث بازگشت قطعه به حالت «راحت» و بدون تنش میشود.
نرمالیزاسیون(نرماله کردن )
نرمالیزه کردن شبیه به فرایند بازپخت میباشد با این تفاوت که زمان کمتری به آن حرارت داده شده و سریع تر خنک کاری میشود. این کار باعث ایجاد فولادی نسبتاً مستحکم تر و سختتر از فولاد بازپخت کامل شده میگردد اما شرایط آن به فولاد بازپخت شده نزدیکتر از فولاد برگشت داده شده میباشد. معمولاً اگر نیازی به ساختاری کاملاً یکپارچه در تمام نقاط قطعه نباشد به جای بازپخت کامل (که طولانیتر بوده و نیاز به انرژی و درنتیجه هزینه بیشتری دارد) از نرماله کردن استفاده میشود.
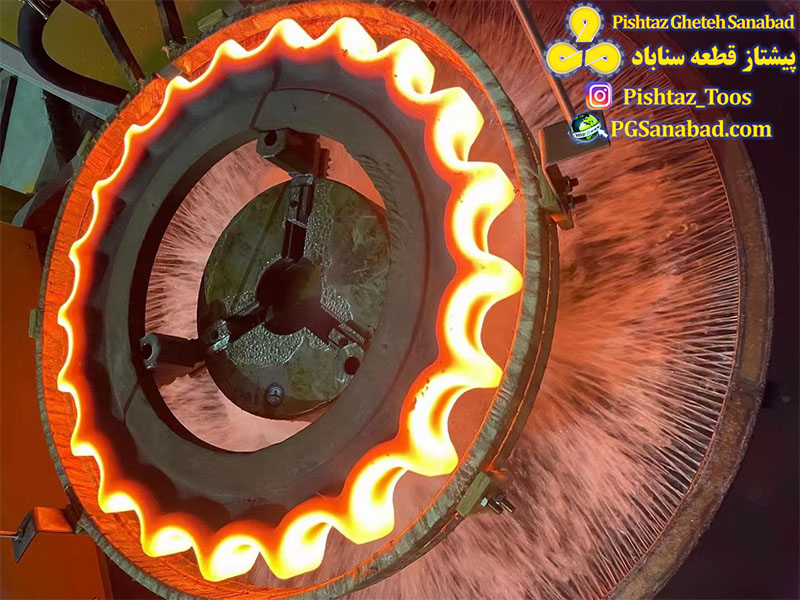
عملیات تنش زدایی
اعمال نیرو یا تغییرات دمایی میتوانند در قطعه تنشی ایجاد کنند که ممکن است بسیار زیان بار باشد. این تنشها که «تنشهای باقیمانده» نامیده میشوند، میتوانند سبب تاب برداشتن، ترک برداشتن یا شکست زودهنگام در حین تولید یا در حین کار شوند. از عوامل تشکیل چنین تنشهایی میتوان به موارد زیر اشاره کرد:
الف- وجود شیب حرارتی یا در واقع عدم سرد شدن یکنواخت قطعه.
ب- ماشینکاری و کارسرد هدف از عملیات تنشگیری آن نیست که تغییرات عمدهای در خواص مکانیکی قطعه اتفاق بیفتد.
در این عملیات از سازوکار بازیابی استفاده میشود و و در واقع تبلور مجدد و تغییرات ریزساختاری در آن انجام نمیشود. به منظور تنش زدایی، قطعات را طی زمان مشخصی زیر دمای A1 گرما میدهند. زمان گرما دهی بستگی به دمای عملیات و ابعاد قطعه دارد. هر چقدر که دمای تنشگیری بالاتر انتخاب شود نیاز به زمان کمتری برای عملیات وجود دارد. در این عملیات نرخ گرم شدن و سرد شدن قطعه باید آهسته باشد تا تنشهای حرارتی جدیدی به قطعه اعمال نشود. این عملیات حرارتی به منظور کاهش یا برطرف کردن تمامی تنشهای ایجاد شده در اثر عملیات تغییر شکل سرد یا در عملیات جوشکاری انجام میگیرد.
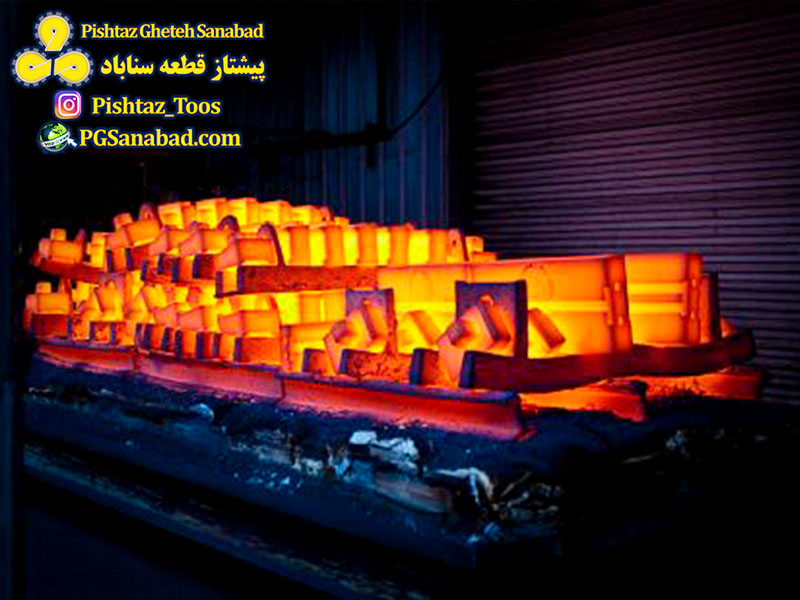
دو نوع عملیات تنش زدایی میتوان انجام داد:
نگهداری طولانی (۱۰ الی ۲۰ دقیقه به ازای هر میلیمتر ضخامت) در دمایی بین ۲۰۰ تا ۴۰۰ درجه سلسیوس، و خنک کاری آهسته آن. مزیت این عملیات این است که هیچ فاز جدیدی شکل نمیگیرد.
برای گریدهایی که مستعد خوردگی بین دانه ای نیستند، نگهداری کوتاه مدت (تقریباً ۳ دقیقه به ازای هر میلیمتر ضخامت) در دمای تقریباً ۸۵۰ درجه سلسیوس.
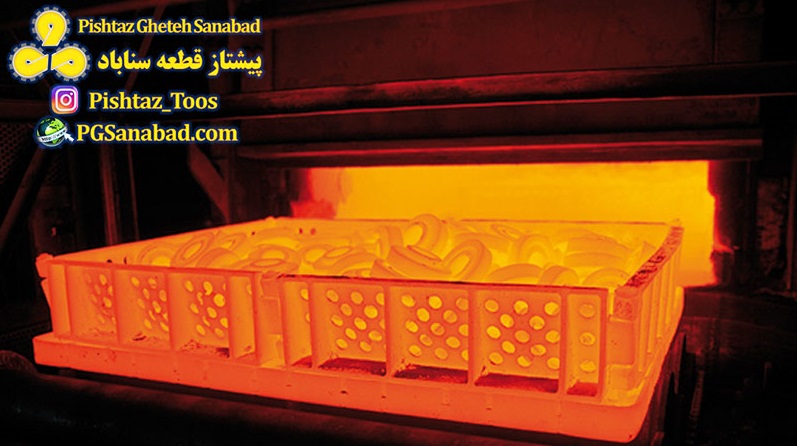
کروی سازی
اسفرویدیت زمانی تشکیل می شود که فولاد کربنی به مدت بیش از 30 ساعت تا دمای 700 درجه سانتیگراد (1300 درجه فارنهایت) گرم شود. اسفرویدیت می تواند در دماهای پایین تر تشکیل شود، اما زمان مورد نیاز به شدت افزایش می یابد، زیرا این فرآیند یک فرآیند کنترل شده با انتشار است. نتیجه این عملیات ساختاری از میله ها یا کره های سمنتیت در ساختار اولیه است (فریت یا پرلیت، بسته به اینکه در کدام سمت یوتکتوئید قرار دارند.
هدف این عملیات نرم کردن بیشتر فولادهای کربنی و امکان شکل پذیری بیشتر آنهاست. فولاد ساخته شده به این روش، نرم ترین و انعطاف پذیرترین نوع فولاد است.
ب) سختکاری سطحی
بهطور کلی روشهای مورد استفاده برای سخت کردن سطحی به دو گروه عمده تقسیم میشوند.
در روش نوع اول تلاش بر تغییر ترکیب شیمیایی لابه خارجی بوده که با استفاده از نفوذ صورت میگیرد که به عملیات حرارتی-شیمیایی معروف است. در این روش سعی بر آن است که اتمهای خارجی با ویژگیهای مورد نیاز سطح به لایه خارجی سطح نفوذ کند تا سختی لایه خارجی را افزایش دهد. برای مثال به منظور افزایش مقاومت سطحی آهن میتوان ازاتمهای کربن یا ازت یا بهطور همزمان از هر دو استفاده کرد.
در روش دوم مبنا بر این است که ترکیب شیمیایی تغییر نکند پس با عملیاتی روبرو هستیم که همراه با تغییرات فیزیکی ماده است.
ما در گروه پیشتاز قطعه از فرایندهای کربوریزه کردن(Carburizing) بر طبق روش اول و همپنین سخت کاری القایی (Induction hardening) بر طبق روش دوم استفاده می کنیم.
کربوریزه کردن: Carburising
کربورایزینگ عمدتا به یک فرآیند عملیات حرارتی به منظور سختکاری سطحی است که در آن آهن یا فولاد، کربن را در دمای بالا و حضور یک ماده حاوی کربن مانند زغال یا کربن مونوکسید جذب میکند که باعث افزاش سختی فلز خواهد شد.
بسته به میزان زمان و دما، سطح تحت تأثیر می تواند از نظر مقدار کربن متفاوت باشد. با طولانیتر کردن زمان کربوریزه کردن و یا افزایش دما معمولاً عمق نفوذ کربن افزایش مییابد. هنگامی که آهن یا فولاد با سرعت سرد میشود، مقدار کربن بالاتر در سطح بیرونی به دلیل تبدیل از آستنیت به مارتنزیت سخت میشود، در حالی که هسته فلز با ساختار فریتی و یا پرلیتی، نرم باقی میماند.
این فرآیند تولید را میتوان با نکات کلیدی زیر مشخص کرد:
برای قطعات کم کربن استفاده میشود.
قطعات در تماس با گاز، مایع یا جامد با کربن بالا هستند.
در سطح قطعه سختی ایجاد میکند.
هستههای قطعه تا حد زیادی چقرمگی و شکلپذیری خود را حفظ میکنند و عمق سختکاری پوسته را تا 0.25 اینچ (6.4 میلیمتر) ایجاد میکنند.
در برخی موارد به عنوان یک راهحل برای کربنزدایی ناخواسته که در مراحل اولیهی فرآیند تولید رخ داده است، عمل میکند.
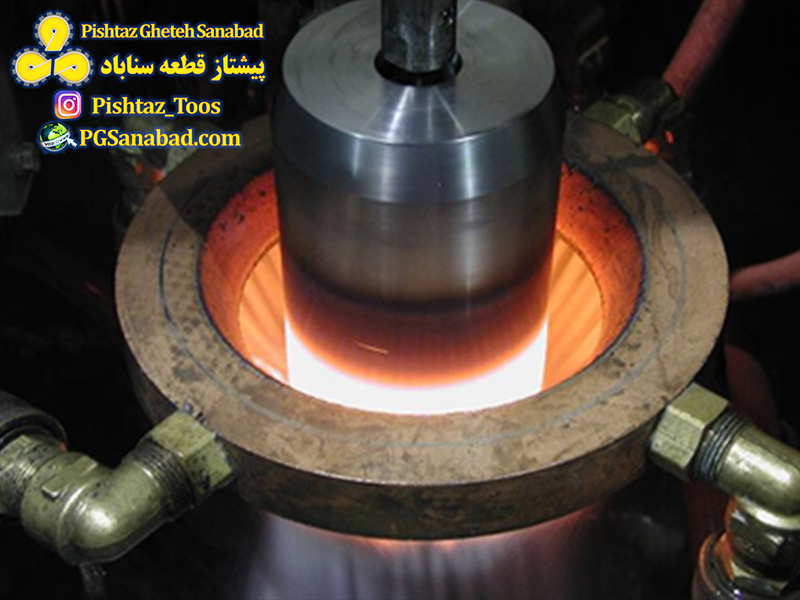
سخت کاری القایی Induction hardening :
نوعی سختکاری سطحی است که در آن قسمتی از فلز به صورت القایی گرم شده و سپس با سرعت بالا سرد می شود(کوئنچ). فلز سرد شده تحت یک تبدیل مارتنزیتی قرار می گیرد و سختی و شکنندگی قطعه را افزایش می دهد . به طور کلی سختکاری القایی برای سخت کردن انتخابی نواحی یک قطعه یا مجموعه، بدون تأثیر بر خواص نواحی دیگر آن استفاده می شود.
در این روش یک جریان متناوب زیاد از طریق یک سیم پیچ هدایت می شود و یک میدان مغناطیسی بسیار شدید و با سرعت در حال تغییر در فضای داخلی حلقه سیم پیچ ایجاد می کند. فلز مورد نظر جهت سختکاری، درون این میدان مغناطیسی متناوب قرار گرفته که در نتیجه تغییر سریع میدان،جریان های گردابی در آن ایجاد می شود و در نتیجه وجود مقاومت داخلی فلز، منجر به گرم شدن آن می شود.
بسیاری از قطعات مکانیکی مانند شفت ها، چرخ دنده ها و فنرها پس از ماشین کاری تحت عملیات سطحی قرار می گیرند تا مقاومت سایشی آنها بهبود یابد. در میان روشهای سخت کاری سطحی، سختکاری القایی یکی از پرکاربردترین روشها برای بهبود دوام قطعات است . این روش در قطعه مورد نظر یک هسته مستحکم با تنشهای پسماند کششی و یک لایه سطحی سخت با تنش فشاری بوجود میآورد که در افزایش عمر خستگی و مقاومت در برابر سایش بسیار مؤثر است .
فولادهای کربن متوسط کم آلیاژ سخت شده با روش القایی به طور گسترده برای کاربردهای حیاتی خودرو و ماشین آلات که به مقاومت سایش بالا نیاز دارند استفاده می شود. رفتار مقاومت در برابر سایش قطعات سخت شده القایی به عمق سخت شدن و میزان و توزیع تنش فشاری پسماند در لایه سطحی بستگی دارد.
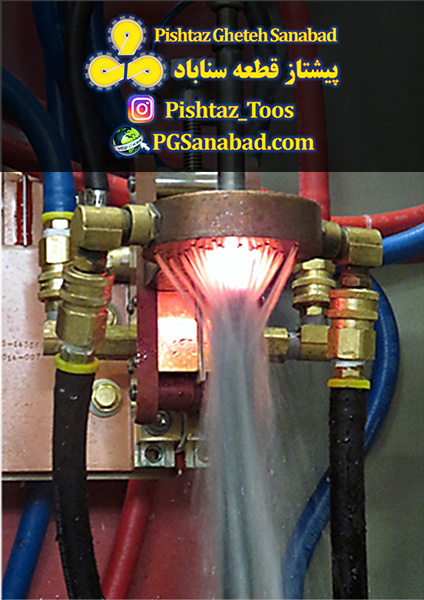